Cold Storage Real Estate Challenges
What challenges and future prospects does the food industry face concerning real estate?
Cold storage warehouses, as opposed to traditional warehouses, are suddenly high in demand because of the steady rise in ecommerce. Online grocery shopping is one of the major reasons why food producers and retailers need cold storages.
In order to meet the growing demand for cold storage warehouses, existing logistics companies need to increase their outdated facilities and expand their space by 100 million square feet or more. This is because according to the Food Marketing Institute and Nielsen, online grocery sales will account to up to 22% of the total grocery sales in the US.
The spurring demand for cold storage warehouses in the US brings real challenges for the real estate industry. The following are the challenges and future prospects for cold storages.
Challenges of Cold Storage Real Estate
The need for new cold storages is eminent. Currently, about 2-3% of the total real estate industry in the US is made up of cold storage facilities. While this number is expected to rise, the following are the factors that hinder this growth.
Finding Space
Finding space for cold storage facilities in the US is very difficult. Most densely populated cities in the US have the highest demand for online grocery shopping. This makes it difficult for builders to find a space in the metro that can be closer to the residential areas. Cold storage facilities that are away from the city are not suitable for perishable goods.
High Costs
Another challenge is the high cost associated with building cold storage warehouses. The average cost to build such a facility is reported to be 40% higher than a traditional, dry warehouse. The costs include insulated metal paneling, cooling equipment, rooftop equipment, subfloor heating, safety and security measures, and other mechanical equipment that is constructed within the warehouses.
Outsourcing
Since 79% of cold storage logistics are outsourced and only 21% are built in-house, logistics’ companies find it hard to meet the growing demand.
Construction Timeline
Cold storage warehouses require technical and mechanical expertise, which is why its construction takes extra money and cost as compared to a traditional warehouse. Normally, construction of a cold warehouse will take four to five months or more.
Difficult to Maintain
The maintenance of cold storage warehouses is extremely challenging. According to the different types of goods stored, the temperatures need to be adjusted and monitored constantly. Generally, the temperature in these facilities should be between -25 degrees and +55 degrees. Maintaining and controlling temperatures require additional equipment and technicians.
Future Prospects
Because of these challenges, the US cold storage industry makes only 2% of US office real estate. While at the same time, real estate market experts suggest that given the multi-billion dollar online grocery shopping industry, there will be a significant rise in the real estate space for cold storage facilities. Builders will have to come up with creative solutions to manage the required storage space. Plus, research has shown that large cold storage warehouses will be constructed in big cities such as New York and Los Angeles.
The growing consumer trends and buying attitudes are encouraging builders to invest in new warehouse technology and construction strategies.We offer cold storage track and trace solutions to meet the demands of today's logistical challenges. Talk to one of our Printer & Barcode Technology Specialists now (800) 643-2664 .
Related Links:
https://www.midcomservicegroup.com/what-thermal-barcode-label-works-in-freezing-conditions
https://www.midcomservicegroup.com/labels-ribbon-printheads#labels
https://www.midcomservicegroup.com/refurbished-thermal-label-printers
https://www.midcomservicegroup.com/refurbished-barcode-scanners
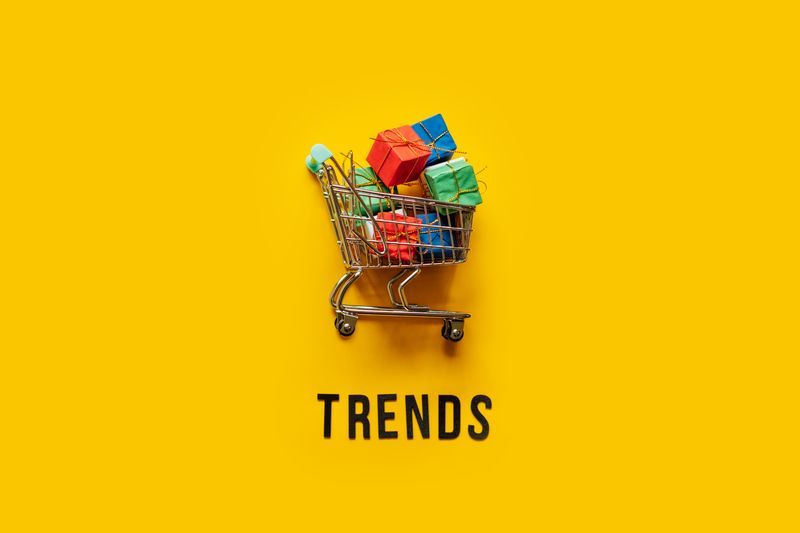