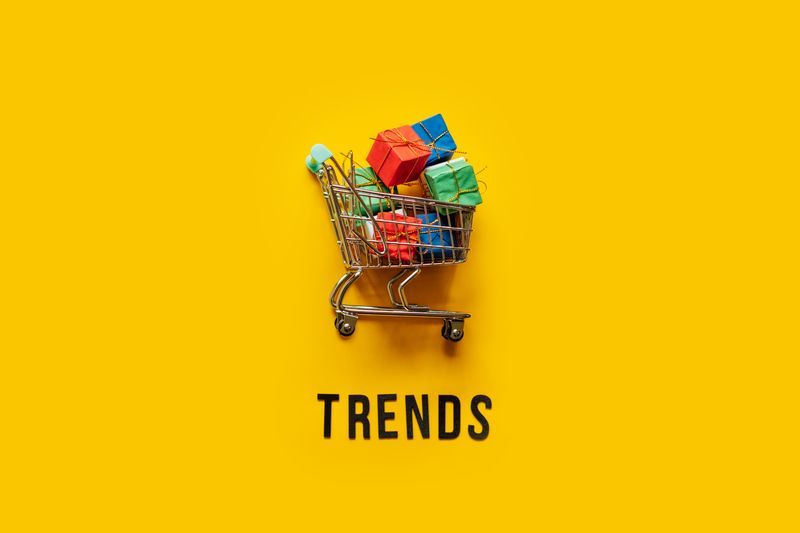
I know what you are thinking … it’s a printer why am I insuring a printer? Well, for one, printers are underrated in terms of importance. People don’t tend to realize what damage a broken down printer can cause, and it can cause enough damage to shut down some business production.
If you don’t believe me, look around the room you’re in right now. Look at everything that has some type of printing on it, especially the documents you received today. Any info on those you would not have received if your printer went out. That’s just the effects of it shutting down. If I were to tell you what exactly could go wrong with every individual printer, like the mayhem guy on the insurance commercials, I would be here all day.
Many printer repair companies offer two types of service; a service repair center (depot) and on-site service. It is great that these services are available, but still after a couple breaks and malfunctions, it can add up especially if there are parts involved. Printer service contracts can help control these costs.
You would never drive your car without it being insured so why would you not cover your printer as well. No worries, I get what you’re thinking. Why should we listen to some guy with just an opinion, we want to see facts. And, in that case, I say “you better get comfortable because this one is going to be a long one.”
Let’s first start with the basics. If you pay for a printer service contract, you get free printer repair for whenever your printer breaks down within the contract time. That’s cool, that’s fine, but what if it happens again? Well, a printer service contract will still cover it. That’s right. With a printer service contract you will still be covered and it will be repaired every time it breaks while under contract. It even beats car insurance.
Every time your car insurance has to pay for an accident repair or any other repair that they make, they end up raising their rates. Most printer repair contracts don’t raise their rates due to excessive service calls. If you do go with the on-site repair you will be responsible to pay the full amount just like any repair on an uninsured car.
We are not done yet though, because there are more than just the service fees for the printers. There is the cost of parts as well. When you are covered under a printer service contract, all replacement parts are covered with the exception of consumables (such as toner or ribbons). This I will admit is a hit or miss type of perk. Sometimes the parts are not that expensive and paying for them won’t hurt your wallet that much.
However, some of the parts can run very high so paying for those can be very hurtful to your wallet, not to mention that even if you are paying for the other parts that aren’t very expensive you are still paying for parts that you wouldn’t have to be if you were covered under a printer service contract. In addition to the cost of parts, there are multiple benefits and cost reducers hidden within the contract that you could be saving right now. Did I mention this was going to be a long one?
The next is the labor cost. When covered by a printer service plan the service company will know what problems your printers have had in the past and what those can end up leading into. So when the service technician does end up coming on-site, the problem can be determined and fixed right then and there on the first visit. Good printer service contract companies should be able to fix a printer on the first trip 80% of the time. In fractions, that is 4/5. So 4 out of every 5 service calls are repaired on the first visit. Now if you don’t have a printer service contract there is a greater chance that you will be in the 20%, or that 1 out of 5 calls will be you, and not only will you have to pay for the first trip out but you will also have to pay for the second trip out, and if it doesn’t get diagnosed until the second trip out then you will probably have to have the tech come out for a third time for installation. So you will end up paying for three trips out including the parts as well, all of which would be of no cost with a printer service contract.
I have a slight confession to make. I did get a little ahead of myself. There is a slight reason why the people who have a printer service contract have such a high first service request rate. This is because, if you have a contract, the techs carry common parts for your printers with them. So that if it is a common problem they’ll have a part right then and there to replace it with and get you back up and running. Which for normal service calls, they might not have causing them to have to order it and come back, which is more time that you have to pay for. And, this is in addition to the part you would have to pay for as well as the downtime for that printer while that part is shipped which would could possible lead to loss of revenue of your own business.
That brings up another point and that is priority response. If you are covered under a printer service contract then you have priority response over just normal time and material service calls. A good printer repair company should have an 8-hour or less response on their service calls, which means you could possible get same day service. It is possible to get same day service for non-service contracts, but there is significantly less of a chance that it would happen especially with the contracts taking priority. This equates to less down time for the printer service contracts than the normal service calls and downtime can never really be good. If you have a backup printer it is not the end of the world, but if you don’t it could seriously cripple your business.
So let’s recap, really quickly. If you get a printer service contract, you get free unlimited printer repair services for the duration of the contract, free parts with the exception of the consumables, an 80% first visit repair rating, common parts for your printers carried on hand, and an 8-hour or less priority response time. This will ultimately save you on parts, service, and downtime along with the loss of revenue that comes with it.
So there you have it. How did I do? Did I convince you? Printer service contracts are the printers’ auto insurance and just like in the mayhem commercials, you will never know when disaster will strike and break your printer. How you will fix it is up to you. I do know one thing though it won’t fix itself!
So get a printer service contract from a reliable printer repair service company and you won’t be sorry. As always, you can call MIDCOM at (866) 504-6631 and talk to a friendly Printer & Barcode Technology Specialist today.
Contract Customer Request Forms